Maximum competence for mould production
Once the design is approved, the mould is physically produced, milled and assembled to perfection in every component, taking advantage of the operators' great expertise in the use of machinery. The company's great flexibility allows our technicians to carry out continuous modifications and improvements, guaranteeing the customer a final product that satisfies him in every respect.
Every medium-sized mould that is produced in the OMP Perego facilities undergoes a careful testing phase. Precise and scrupulous checks carried out by highly qualified personnel ensure that the finished product fully meets the customer's requirements.
When the testing phase is over, the OMP Perego production unit will put the mould on line, checking its functionality and, if necessary, making any final modifications, impeccably closing a production process guaranteed by ISO 9001:2008 certification
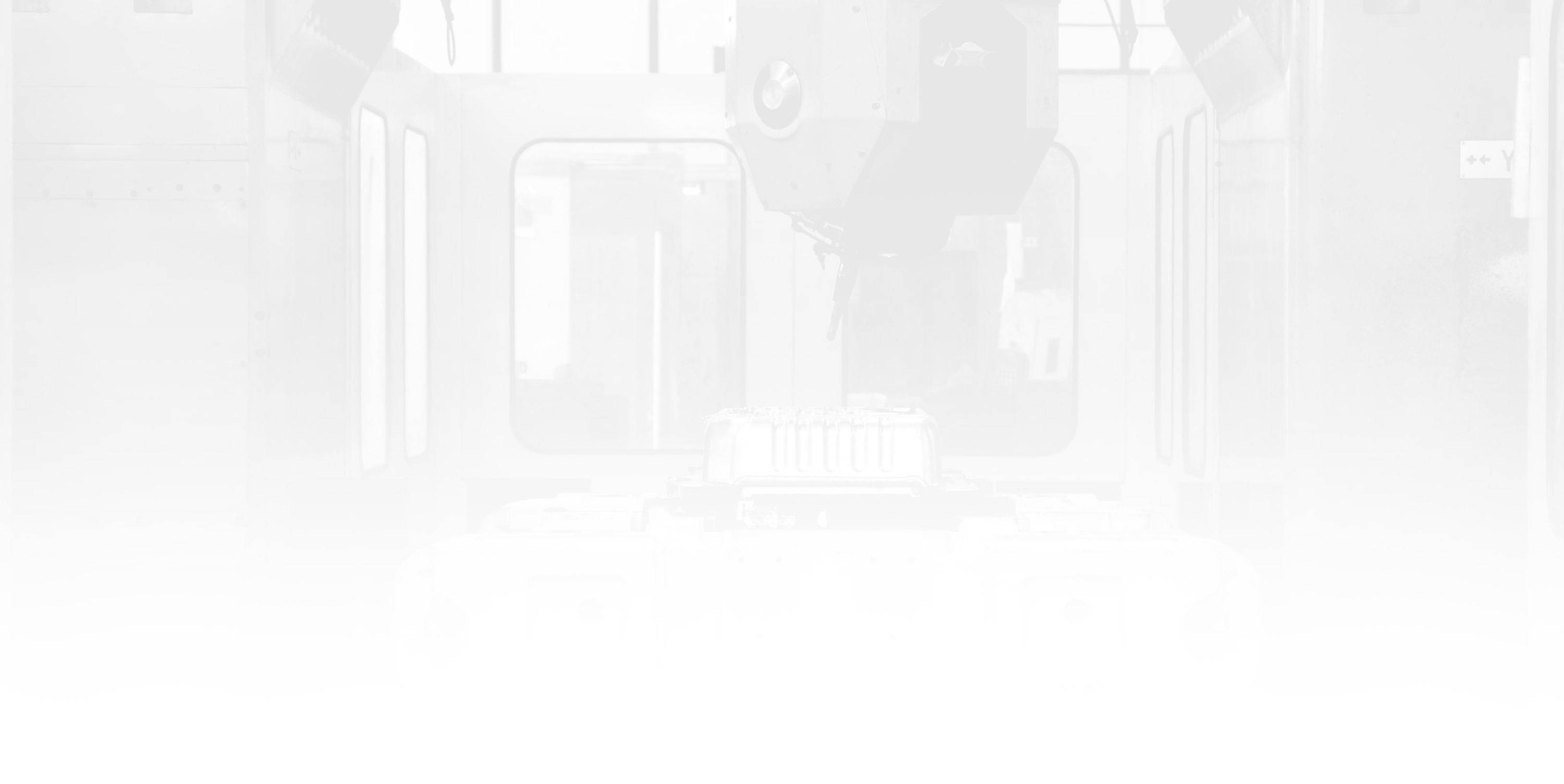
Precision technology and machinery
OMP Perego is a company with a clear eye on the future. With this in mind, the company continues to make investments and improvements in its modern machinery fleet, offering customers innovative solutions and workmanship.
The company's machine park includes four vertical machining centres, three different types of milling machines, one EDM machine and two quality control machines.
The company also has three hydraulic presses - maximum capacity 2000 tonnes - and three mechanical presses with a maximum capacity of 800 tonnes.
Set-up
Tuning is a crucial step in the mould-making process and consists of two main steps. The first step involves adjustment and checks to ensure the functionality of the mould and to obtain a stable and repeatable geometric result. The second step consists of introducing appropriate geometric corrections to ensure that the final part meets the quality standards required by the customer.
In this phase, manual work and the skill of the workers are crucial. The precision and skill of the workers in making adjustments and checks are essential to the success of the fine-tuning process. After completing these operations, the mould is equipped with all necessary pneumatic and electrical systems. Finally, the mould is painted and completed with lettering and name plates before being shipped to the customer.
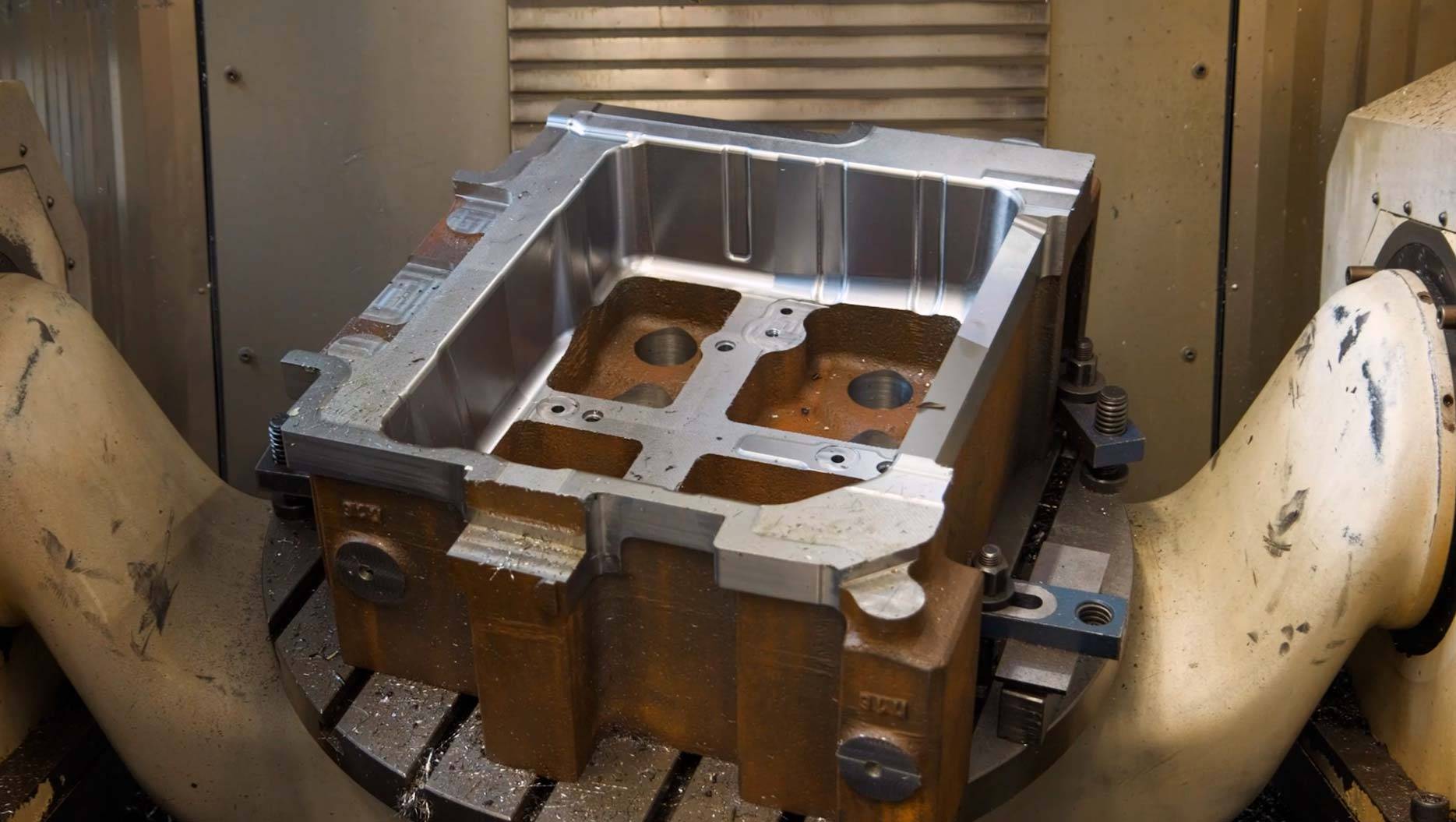
Vertical Machining Centres
- SUPERMAX MOD V2610B BY MY-VAL (2600x1020x760)
- ZPS MCFV 1260 TREND (1250x650x650)
- ZPS MCFV 125 EX (1250x650x650)
- ZPS NCFV 1680 (1650x810x810)
Portal milling machines
- EUMACH DVM 4025 (4800x2800x1100)
5-axis moving column milling machines
- n.2 SORALUCE FP 6000 (6000x2100x1300)
- DEBER AFC130 PERRUCCI + TURNTABLE (3000x1900x2000)
5-axis high-speed milling machines
- JOBS JO MACH 141 WITH HIGH-SPEED MANDRINO (3400x2700x1250)
- RAMBAUDI (4200x2500x1200)
- REMCONTROL WITH ROTARY TABLE
- MITSUBISHI FX30 (800x575x215)
Hydraulic presses
- MOSSINI (5000x2500x2400 - max T.2000)
- EMANUEL MANZONI (3200x2000x2000 - max T.800)
- MOSSINI (4000x2500x2200 - max T.1200)
Mechanical presses
- INNOCENTI MOD S2400 0860 (2700x1500x90 - max T. 400)
- GALLI MOD. 80 ML 300 (3000x2000x1300 - max T. 800)